In a major, high-value project – the second at this particular plant in Mexico – NUTEC Bickley will supply a 125m-long tunnel kiln to one of the world’s leading advanced ceramics manufacturers.
Technology
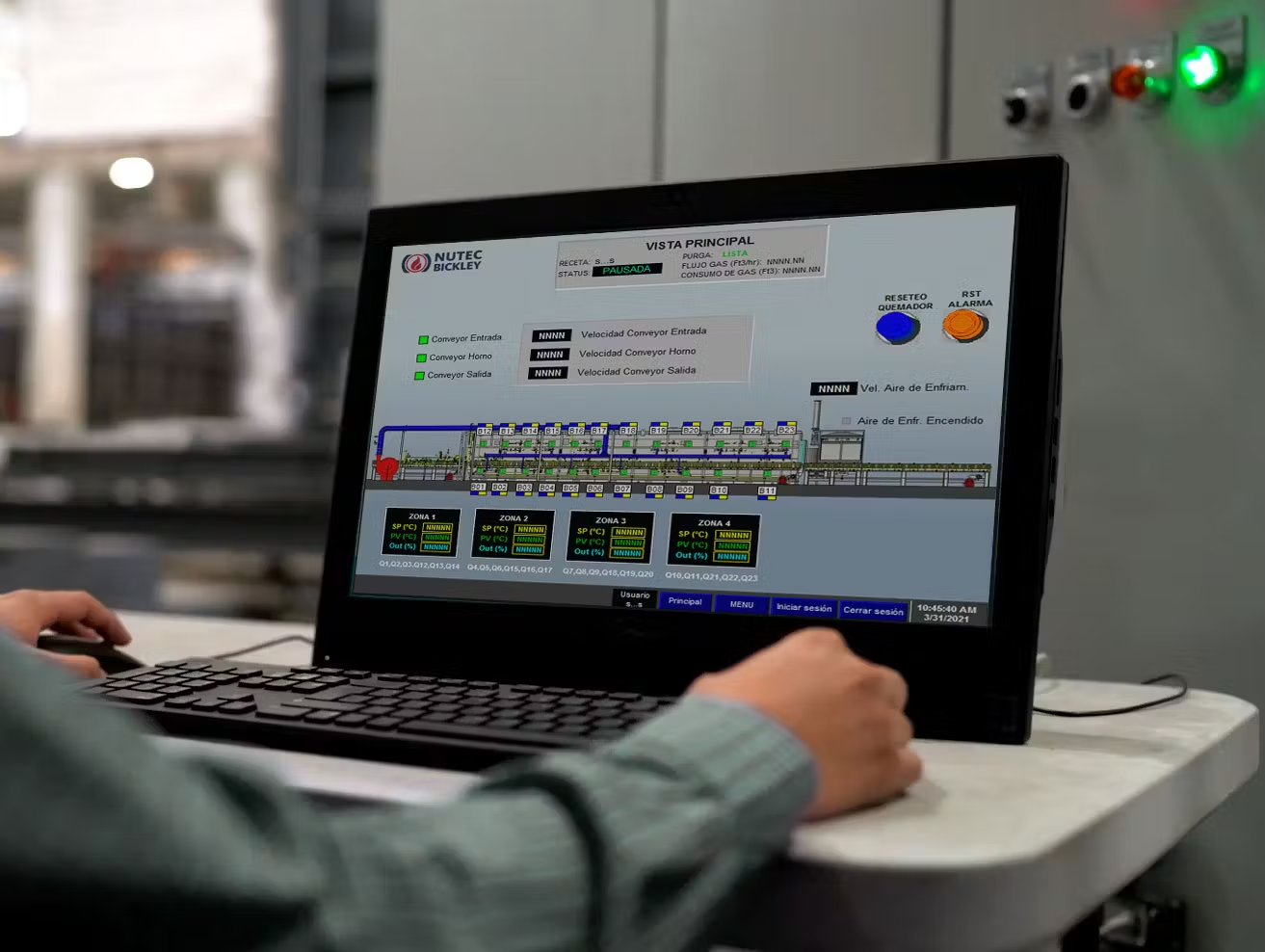
SCADA
With our SCADA systems, kilns operators are able to have complete control of their firing process, enhancing efficiency and productivity.
Learn more about SCADA
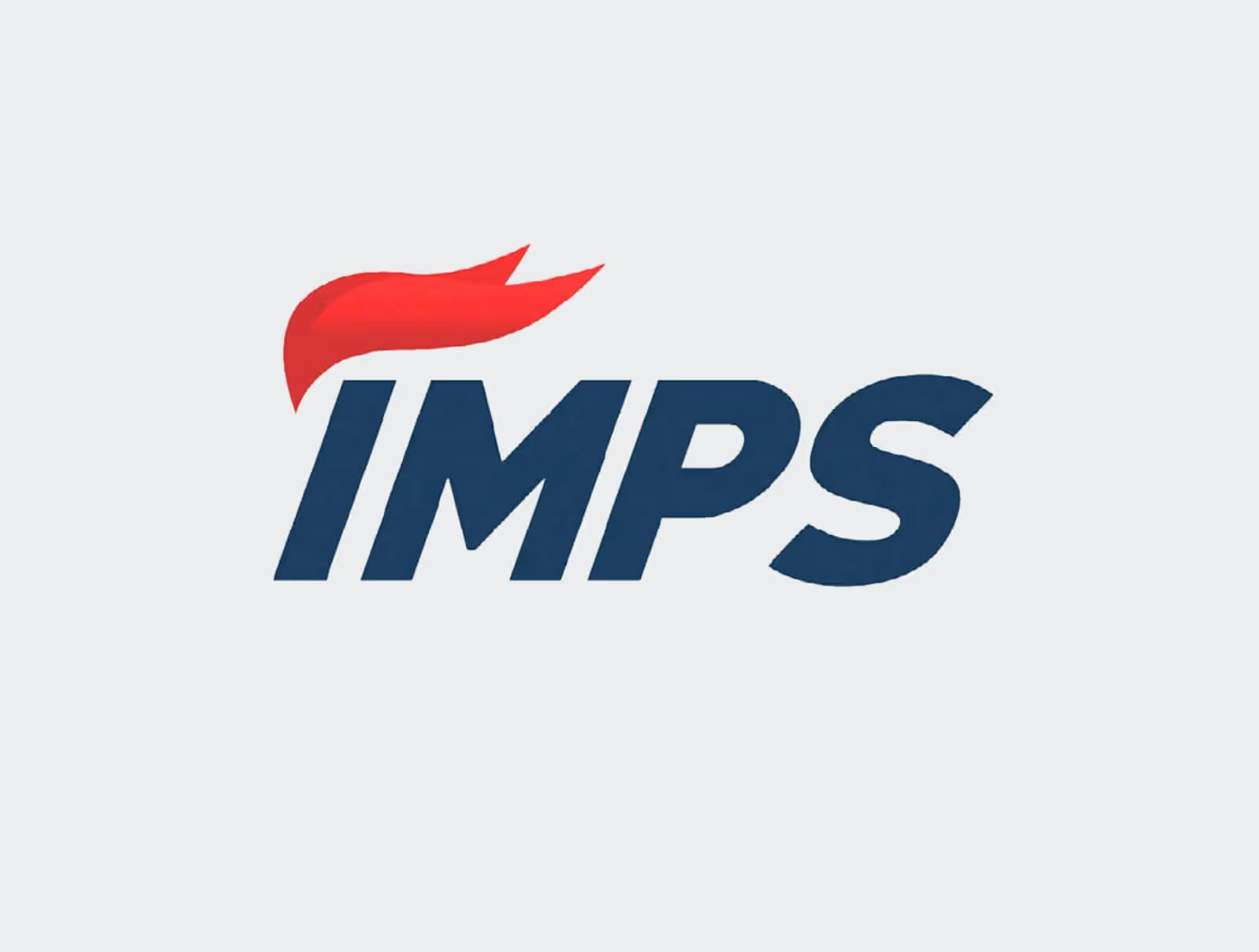
IMPS™
NUTEC Bickley’s unique firing and cooling pulsing control system provides a perfect solution in relation to temperature uniformity as well as fuel efficiency.
Learn more about IMPS™
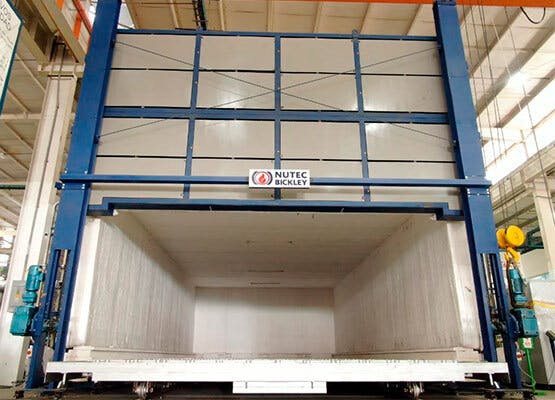
Jointless® Insulation
NUTEC Bickley’s patented ceramic fiber Jointless® modules provides for minimal maintenance, enhanced fuel economy and extended service life.
Learn more about Jointless® Insulation